The Ultimate Guide for
Blast-Resistant Buildings
What You Should Know Before You Buy
You Have Questions
Maybe you've been through a facility siting study, or maybe you know you need to add occupied space at your refinery. Or, it could be time for a planned shutdown, and you're going to be bringing in a lot more contractors. For those reasons or many more, you need to invest in a blast-resistant structure. But, before you pick up the phone to start making calls or send that email, let's look at all of the considerations you'll need to make.
We Have Answers
As the industry leader in blast-resistant modular buildings, RedGuard takes pride in sharing the wealth of information we've gained since becoming one of the industry's first manufacturers of blast-resistant buildings. We’ve put together The Ultimate Buyer's Guide for Blast Resistant Buildings, but you can also check out individual topics in our Learning Center.
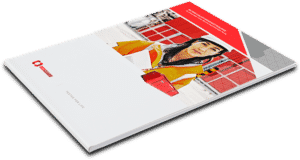
DON'T HAVE TIME TO READ IT NOW?
Fill out the form for a downloadable PDF that you can keep and reference later. Or, simply keep scrolling to read without submitting your email.CHAPTERS
- 1 -
What is a blast-resistant building?
THE BASICS ABOUT BLAST-RESISTANT BUILDINGS
A blast-resistant building is a structure that has been designed to withstand significant blast events. These buildings are often constructed with thick steel walls and interior features and fixtures designed to withstand the heightened psi levels associated with small to large blast events. Sometimes they are referred to as blast-resistant modules, blast-resistant units, or simply as a BRB or BRM. They are often found in oil refineries, chemical processing plants, or similar operations.
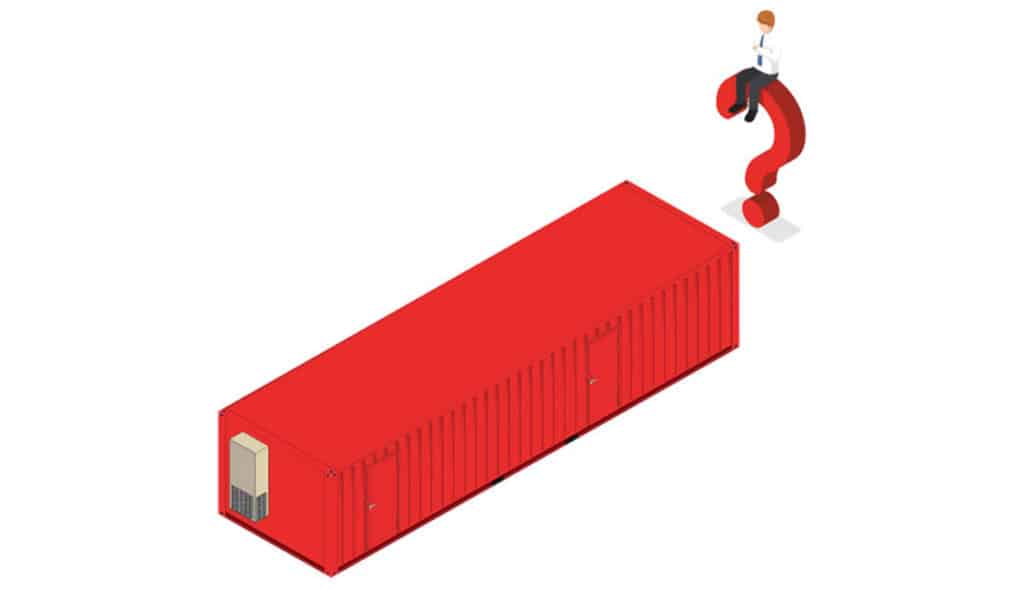
WHAT ARE THE REGULATIONS COVERING BLAST RESISTANT BUILDINGS?
There are no official regulations that cover blast-resistant modular buildings. There are some recommended practices laid out by the American Petroleum Institute that cover permanent and portable structures that are located within blast zones. These are known as API RP 752 and 753. They ensure that occupied buildings protect against potential hazards by recommending specific blast response ratings to protect occupants from potential hazards in hazard zones.
As a safety authority in blast resistance, RedGuard recommends using only blast-resistant buildings with a low or medium response rating (meaning low- to medium- damage after a blast event). While still considered “blast resistant,” a building with a high response rating could sustain structural damage during a blast event and may even collapse due to environmental conditions. We’ll talk more about what “high response” means in Chapter 3.
- 2 -
What dangers are there to people during a blast event?
Why blast resistant buildings?
Those who work for oil and gas companies take on a certain amount of risk. Because of this, companies should take the steps needed to protect them from as much risk as possible. This chapter will examine how a refinery explosion affects the human body and how a blast-resistant building can prevent injuries and mitigate the risk.
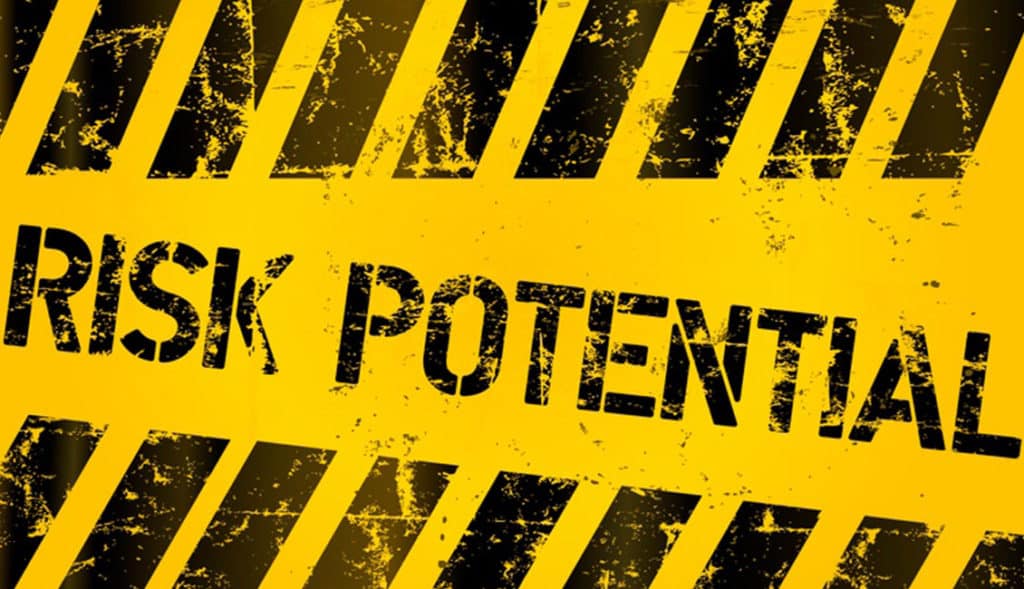
HOW DOES A BLAST AFFECT THE HUMAN BODY?
The effects of a blast event on the human body will depend on several factors, a person’s proximity to the center of the explosion, the terrain and surroundings within the area of the blast, the cause of the explosion (i.e., the type of gas or other material that caused the event), and the intensity and frequency of displacement waves.
With these factors in mind, it is important to note that the human body can typically survive high blast overpressure. For example, a 5 psi blast overpressure can rupture eardrums, while lung damage can occur at an approximately 15 psi blast.
One significant factor that must be considered when taking precautions to protect personnel during a blast event is the impact of blunt force trauma to the human body. Injuries like these can occur with overpressure as low at 1-2 psi, when windows may shatter, and debris is thrown. Crush injuries may occur at slightly higher response levels when the building’s structural integrity begins to fail.
In a blast event, or explosion, the human body might be thrown, large objects might be propelled at a person, and light objects can quickly become speeding projectiles. Fortunately, a blast-resistant building is designed to protect people from the aforementioned injuries.
A blast resistant building that has the right psi ratings for its intended use and location within your facility can not only protect personnel during blast events; it can also save lives and reduce the risk of nonstructural items causing bodily harm in the aftermath of a blast event.
Because there are so many people involved in oil and gas processing, the financial risk of NOT protecting them as they do their work is huge. Understanding the financial impact of a blast with real-world examples is essential. To do this, let’s take a look at the trickle-down continuous financial costs of a blast event.
UNDERSTANDING THE FINANCIAL IMPACT OF A BLAST EVENT
One of the easiest ways to understand the long-term financial impact of a blast event within the oil and gas industries is to explore historical incidents.
- On May 5, 1988, in Norco, Louisiana, a refinery experienced a blast event that caused 42 injuries and seven fatalities. The major blast event hurled debris as far as five miles away. The incident itself was heard nearly 25 miles away in New Orleans. The total estimated cost of the event was $706 million. The latter funds were used to pay for property damages, injuries, rebuilding, an investigation, and other components directly related to the event.
- On March 23, 2005, in Texas City, Texas, one of the world’s largest refineries experienced a blast event that caused 180 injuries and 15 fatalities. The cost of this blast event included an Occupational Health And Safety Association (OHSA) imposed $87 million fine (due to 700 safety violations found during the investigation into the incident) and an estimated $2 billion for repairs and compensation.
THE REAL IMPACT OF BLAST EVENTS
As seen in the proceeding two events, the far-reaching impact of oil and gas blast events extends beyond structural costs. In fact, the effects of a blast event on the human body can result in expensive medical bills, workers compensation, paid time off, and (if warranted) legal compensation. Additionally, as seen in the Texas City refinery blast event, a failure to meet specific safety standards can result in hefty fines. In this vein, oil and gas companies should take the necessary safety precautions to a) protect against blast events and b) protect their structures and workers from the negative physical and financial impacts of blast events.
One way companies and facilities can protect their structures and personnel is to use blast-resistant buildings. These resilient structures will protect personnel from bodily harm, save lives, reduce the risk of nonstructural items causing physical injury or property damage, and reduce the financial impact of a blast event.
- 3 -
What is response level?
Is high response acceptable?
When it comes to blast-resistant buildings, the industry’s manufacturers will often use the term response level to predict the extent of repair needed on a building after an explosion. This section defines what each response level is, and what to look for in a blast-resistant building.
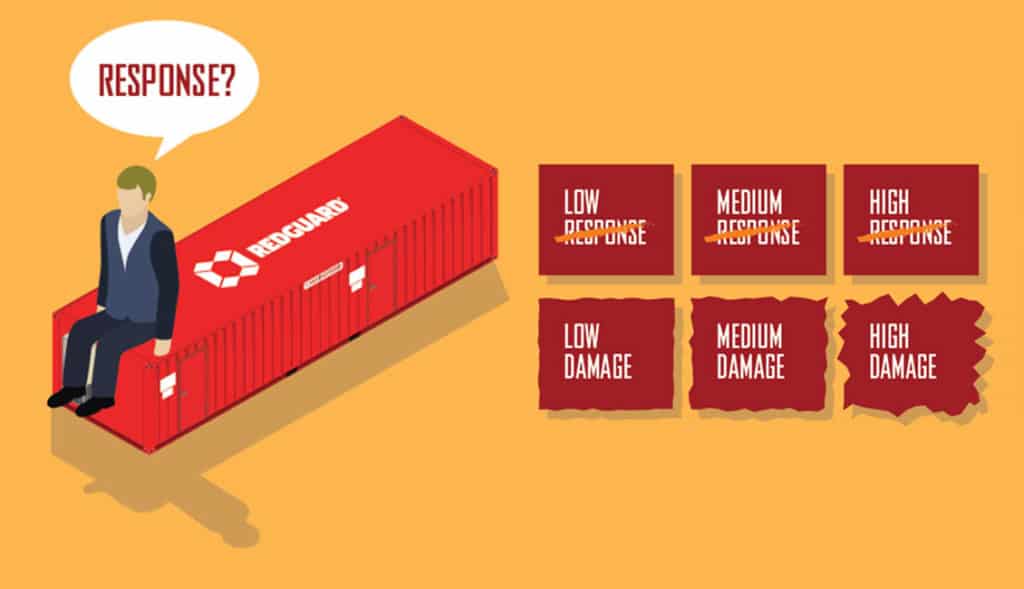
WHAT IS RESPONSE LEVEL?
Blast response levels are ratings established by the American Society of Civil Engineers (ASCE) to predict the extent of repair resources that would need to be devoted to a building after an explosion. Their descriptions include:
Low response — Localized building and component damage; the building can be used, however, repairs are required to restore the integrity of the structural envelope; and the total cost of repairs is moderate.
Medium response — Widespread building/component damage; the building cannot be used until repaired; and the total cost of repairs is significant.
High response — Building/component has lost structural integrity; a building may collapse due to the environmental conditions, and the total cost of repairs approaches replacement cost of the building.
Substitute the term "damage level" for "response level," and you have an instant picture of what these ratings mean. Given the options of low damage, medium damage, and high damage, you obviously don't want to be working in an area that is highly damaged during a blast event.
WHAT TO LOOK FOR IN A BLAST-RESISTANT BUILDING
Anything worse than medium response is virtually synonymous with injuries and fatalities. And suppose you plan on using the building to house critical control systems in a petrochemical facility. In that case, casualties are only one of many problems you'll face in a high response situation.
WHAT ABOUT BLAST TESTING?
The final proof is in the testing of the blast-resistant design. RedGuard was one of the first companies to do a field test of our design. We put a high priority in looking at the design and analysis of blast-resistant structures. In our original blast test, we detonated 1,250 pounds of high explosive ammonium nitrate/fuel oil charge at a standoff distance of 110 feet from our building. This explosive amount created a blast strength far above the ratings required to meet ASCE low to medium response standards.
The building suffered no structural damage, and neither did the furnishings, office equipment, or the crash test dummy we placed inside. The building is still in use today at the RedGuard headquarters.
This outlines the importance of taking a closer look at both response level ratings and test results before buying a blast-resistant building. In response to the question, "Is high response acceptable?" - the answer at RedGuard will always be a resounding no.
- 4 -
What is blast proof?
At RedGuard, we use the term “blast-resistant” rather than “blast-proof,” and this chapter delves into why. We’ll define those terms and talk about the factors at play in blast-resistance, such as the structure, design and analysis of blast-resistant structures, the building’s material, the building’s proximity to the blast wave, and the duration of the blast.
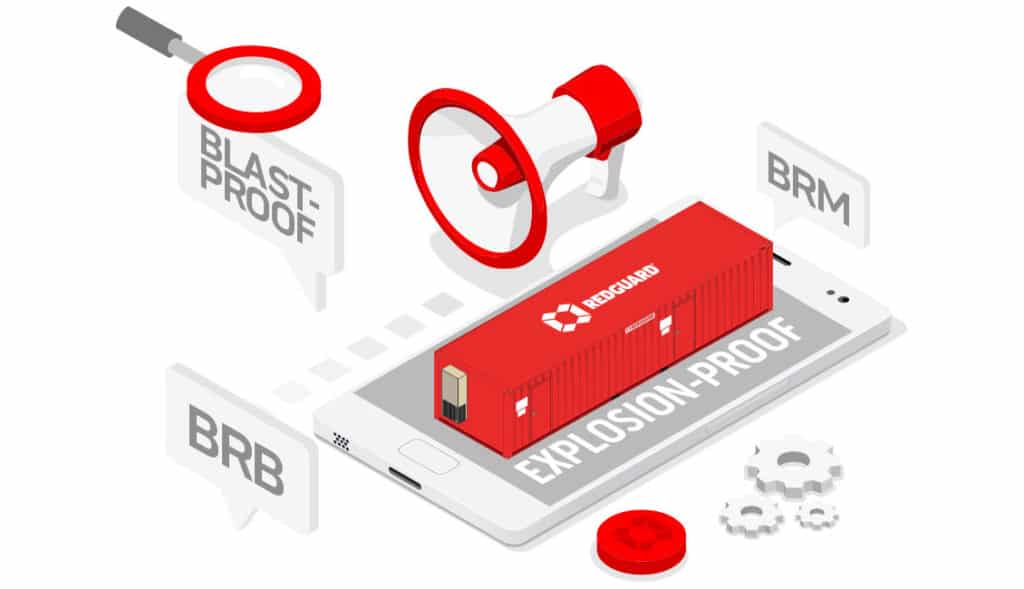
WHAT DOES BLAST-PROOF MEAN?
The word “proof” implies that something is impervious. However, there really is no such thing as a blast-proof building. If you exceed the load that a building is designed to resist, there's a strong possibility that it could fail.
The word “resistant” means that the object can resist some type of hazardous penetration. In our case, the hazard is blasts or explosions, but you may also think of objects that are water-resistant, slip-resistant, heat-resistant, or puncture-resistant.
Blast-resistance has a lot of nuance to its meaning because there are many factors at play that determine the amount of damage during an explosion. Let’s look at the factors in play when it comes to how blast-resistant a building is.
DESIGN AND ANALYSIS OF BLAST-RESISTANT STRUCTURES
We’ll start with structure because the structural engineering of a blast-resistant building is probably the most critical factor in protection. This goes back to those response levels, mentioned earlier in Chapter 3.
Remember High, Medium, or Low Response? All of them are considered blast-resistant, though not all are equal. And none of them would be regarded as “blast-proof.”
Manufacturers of blast-resistant buildings will have different explanations for their design methodology, or why they design to a specific blast response level. Still, it’s important to look at whether they regard structural integrity as a priority, or if they simply meet the minimum requirements to get their building rated.
BUILDING MATERIAL
Hand-in-hand with the structural engineering of a building is the building material itself. Today’s manufacturers of blast-resistant buildings are wise to take lessons from the past. In some of the early blast events that shaped the industry, onsite offices in temporary trailers were completely destroyed, while metal shipping containers inside the blast zone were still standing, their contents intact. Though today’s designs are far more complex and protective, shipping containers became the basis for an idea to create blast-resistant buildings. Extensive engineering helped create a final design that has led the industry in blast resistance.
Blast-resistant builders employ many different structural designs and materials. There are blast-resistant structures that are permanent brick and mortar buildings; there are temporary blast structures, there are even tents, sometimes called air shields; and there are modular buildings made of hardened metals that are either portable for temporary use or anchored for permanent use.
Though many materials can be used in the design, none of them are blast-proof, and their levels of blast-resistance vary.
PROXIMITY TO THE BLAST WAVE
The further you are from an explosion, the less of an impact you will feel. Like structure, proximity to the blast also makes a difference in the damage a building will sustain after a blast. The closer to the blast wave, the stronger the building’s blast resistance should be.
A high response blast-resistant building placed in a hazardous process area would be very dangerous in the event of an explosion, even though it is technically blast-resistant. A low response building in the same area may sustain little to no damage.
Both buildings may be resistant to damage in an explosion, but are either really blast-proof? Not really. The most we can do is prepare for the dangers that we know are present.
DURATION OF THE BLAST
If how close a building is to a hazard and the ruggedness of the building’s structure are vital components to blast resistance, it makes sense that the blast’s duration, or how long it lasts, is also a significant factor. There are some details you can consider when planning for safety.
Manufacturers of blast-resistant buildings usually employ a combination of pounds per square inch (psi) and a duration of time, expressed in milliseconds (msec) that the pressure of a blast is applied. Unfortunately, the terminology is often inconsistent from one manufacturer to the next.
As an example:
- A blast resistant building can be engineered to withstand an explosion of 5 psi for 200 msec.
- That same building could also be advertised to withstand a blast of 5 psi at 500 psi-msec, which would also be a correct calculation.
One description communicates the duration and the other the impulse, or measure of the energy of the blast event (psi-msec). Unfortunately, that difference is lost on many seasoned professionals in the oil and gas industry. The 500 psi-msec impulse appears to signify a more substantial building than the 200 msec duration rating, even though both ratings apply to the same building, with the only difference being what is calculated.
This simple nuance can lead to confusion and possibly cause someone to accept an inferior level of blast protection. It’s essential to understand these calculations and to ask whether the description you see communicates a duration or a measure of energy. Understanding the level of threat that a building can withstand, within a set time, is critical. Be cautious of manufacturers that fail to give you clear information when you ask about the duration of time a building can withstand its psi rating. It’s possible that they don’t understand this nuance themselves.
THE VERDICT ON THE TERM “BLAST-PROOF”
Put this all together, and you can see why the terms blast-resistant or explosion-resistant are the preferred terminologies. Simply put, we don’t say blast-proof, or explosion-proof, because we know that explosions are powerful forces. If you exceed the load that a building is designed to resist, it might fail.
- 5 -
A breakdown of the benefits of blast resistant buildings
In the previous chapters, we talked about the lifesaving benefits to people and the financial benefit to the bottom line. Now, let’s delve into seven benefits of blast-resistant buildings that will help you make an informed decision mitigation options for your facility.
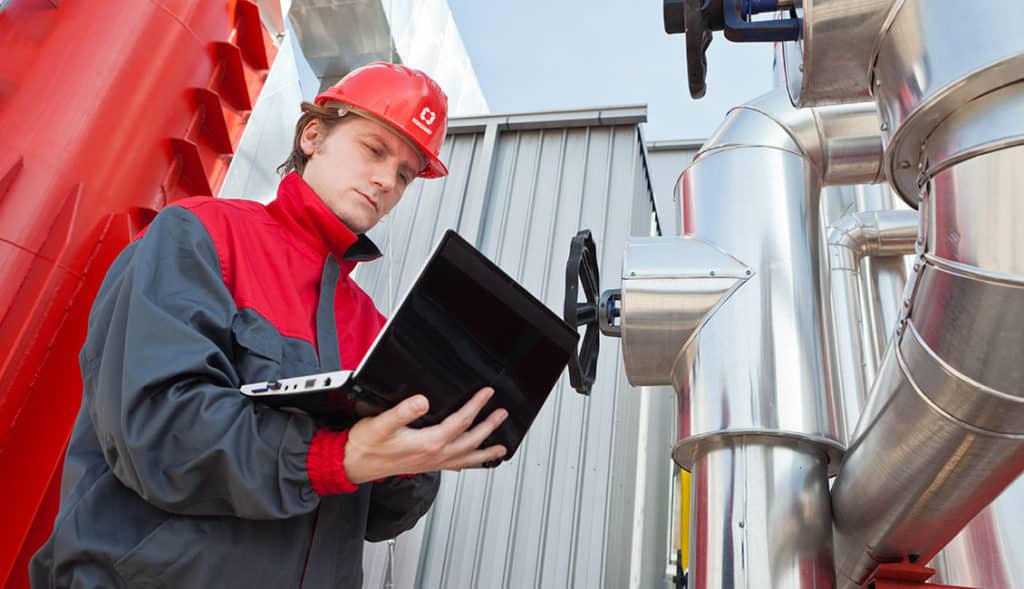
1. STAFF, EQUIPMENT, AND ASSETS ARE PROTECTED DURING A CATASTROPHIC EVENT
Blast-resistant modules, or BRMs, are built to withstand the devastating damage resulting from an explosion. The people, equipment, and assets inside of the buildings will be protected.
The level of damage is all dependent on the blast rating and the building’s proximity to the hazard. If you work in a classified area, in a building with a low to medium response (which, as mentioned earlier, means it would sustain low to medium damage), your chances of survival are much higher than in a soft-sided trailer, which is still used on some worksites.
2. REDUCE LIABILITY, INCREASE PEACE OF MIND
When the risks to human life are decreased, the amount of liability is also reduced. For every significant blast event that has occurred, when there were numerous fatalities or injuries, the investigation to determine cause and fault begins almost immediately.
Including blast-resistant buildings as safe havens or shelters-in-place can give those who work in hazardous areas peace of mind. Should a catastrophic event happen, it can reduce the company’s liability since it took measures to keep its workforce safe.
3. REDUCE TIME LOST TO RETRIEVE TOOLS OR OTHER EQUIPMENT
One benefit of blast-resistant buildings that's often overlooked is the amount of time, and therefore money, that you will save by storing equipment and tools in blast-resistant tool cribs inside the hazardous area.
Some refinery sites are huge. Often, the time required to get into and out of the classified area involves checking in and out and even arranged transportation.
When you store tools and equipment outside of the blast zone in order to keep them safe, employees must make a trip each time a specific piece of equipment must be used or checked out. When you begin to calculate the amount of time spent going back and forth to retrieve tools, you realize the benefit of just keeping those tools closer. Depending on the size of the workforce, the lost time savings could be huge. The amount of time saved over time might even pay for the cost of the blast-resistant building.
4. REDUCE THE AMOUNT OF TIME EXPOSED TO HAZARDS
It goes hand-in-hand with reducing time and money, that each time a worker must travel across a worksite to retrieve a tool, they are spending time exposed to hazards.
Reducing the amount of travel time reduces the time that the workforce is exposed to risks.
5. FLEXIBILITY AND MODIFICATIONS
Modular buildings are easy to modify. If the process area changes after five years, and your facility siting study now shows that the blast zone has changed, you may need to modify existing buildings in order to provide protection.
If your building is a multi-section, this might be a matter of adding additional sections. Alternatively, you may choose to use the existing building and add more buildings to accommodate your need. Modular buildings can even be stacked to save space.
6. MOBILITY
Traditional buildings are permanent structures. Modular buildings, on the other hand, and specifically blast-resistant modular buildings, are built with the knowledge that the ability to move it after it’s been placed on a worksite is of great benefit.
A building may need to be moved to accommodate a facility’s turnaround schedule. A blast-resistant module can be placed on a site to provide shelter for more people during a turnaround, and then removed once the turnaround is complete and the plant returns to its regular operating schedule.
Most oil and gas facilities go through turnarounds every three to five years. Having a permanent structure that is only at peak usage during a turnaround is not economically feasible. Blast-resistant modules can be moved to a different part of a plant to be used elsewhere, or to a completely different location altogether, perhaps for a different turnaround.
The relocation of buildings is also desirable when an area becomes more densely populated. A population swell makes the environment for oil production less safe, both due to natural disasters and the possibility of chemicals in highly populated areas. Many refineries choose to move when the population grows. The ability to transfer the buildings during the move can save millions of dollars in buildings that would otherwise have to be purchased again.
7. BUILT OFFSITE
When a structure is mobile, in addition to the benefits listed above, that also means it can be manufactured off-site and then transferred to the worksite and assembled.
Compared to an on-site, traditional build, where the location will be out of commission for weeks at a time, there will be fewer restrictions on the area’s use since it won’t be tied up in construction for as long. In a traditional build, you may go through a multitude of steps, like:
- Site preparation/grading
- Foundation
- Framing
- Construction, including windows, doors, masonry, etc
- Roughing the electrical, plumbing, and HVAC
- Insulation
- Finishing the interior walls
- Trimming/painting the exterior
- Installation of interior elements like cabinets or workspaces
- Installation of flooring
- Finishing electrical, plumbing, and HVAC
- Connection to water, sewer, or other services
In comparison, the vast majority of the work on a blast-resistant modular building is done before the building leaves the production center. When it arrives on site, the "to-do" list will look more like this:
- Site prep (done before the building arrives)
- Foundation (done before the building arrives)
- External finish of the structure (including welds, if the building is multi-section)
- Finishing electrical, plumbing, and HVAC
- Connection to water, sewer, or other services.
In addition, the process itself is safer, since the skilled labor constructing the building will need to be in a hazardous area for only the amount of time it takes to install it.
- 6 -
How much does a blast-resistant building cost?
If you’ve done your research online, you know that information about the real cost of a blast-resistant building is nearly impossible to find. Let’s examine the factors that affect a blast-resistant buildings’ cost.
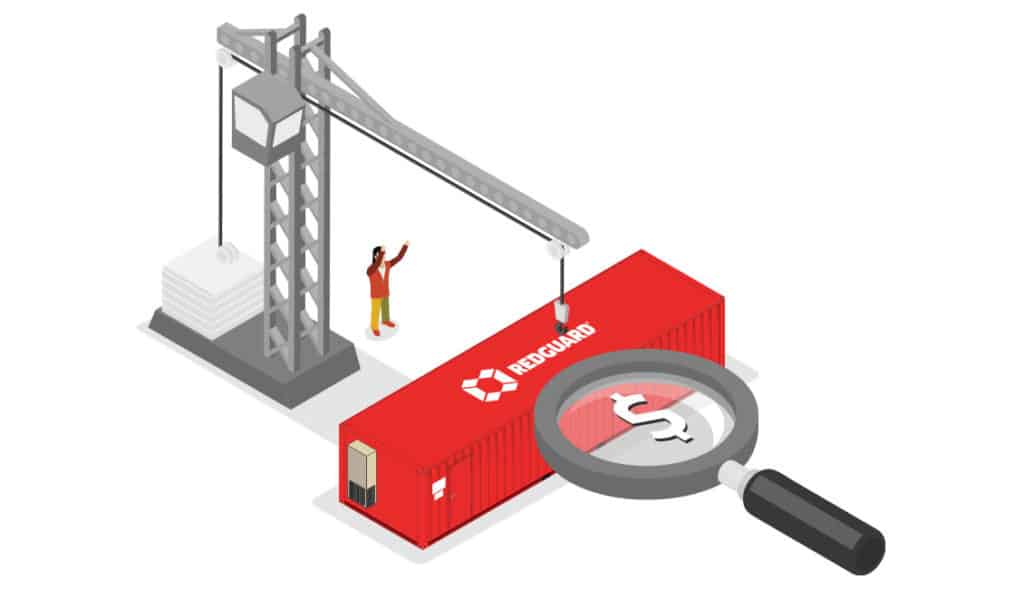
How long the building will be in use:
The length of time the building will be in use determines if the building is purchased or leased, which probably affects the cost most of all.
The location of the building in proximity to hazards:
A building’s location on the work-site makes a difference because, even on one site, areas have varying levels of PSI during a blast event.
The duration of exposure is also considered, typically expressed in milliseconds. You will find that BRBs come in several “response levels,” as mentioned in chapter 3, or are rated for a specific PSI and duration of exposure.
The type and size of the building and the number of units needed:
Many people think that all blast-resistant buildings are the same, but in actuality, a blast-resistant building can be made to look like and function as almost any type of building. (Labs, control rooms, lockers, restrooms, tool cribs, break rooms, and more.) Components of structure will affect the cost.
Since buildings come in different sizes, the building’s size affects the raw materials and again, the cost. When it comes to size, another factor to consider is how much the building’s width and height drive the cost of transportation.
If a lot of space is required, you can consider using one or more buildings, or creating a multi-section building, where several components are placed together to create a larger area.
The number of external doors, and If the building requires windows:
Every component of a blast-resistant building must be properly vetted. The most vulnerable elements of a blast-resistant structure are the windows and doors. (These elements are not dangerous. They just require careful engineering.)
Each component being vetted also means that each component must be blast-tested. It would make no sense to put windows into a blast-resistant building without knowing if they could withstand a blast. So the windows must be blast tested, and when considering doors, the door itself must be tested, as well as the latches and hardware.
Adding windows to the building means that the studs must be cut to accommodate the windows. Cutting the studs of a blast-resistant building means that there is engineering involved to determine that it retains its structural integrity.
When it comes to windows and doors, we must figure the cost of raw materials, and also the cost of engineering required for the placement, to ensure that the building is safe.
The type of interior components required (plumbing, electrical connections, communications, fixtures) as well as the level of interior finish:
All interior components must be rugged enough so that they don’t become projectiles in a catastrophic event. (Projectiles are the primary source of injury and death during blast events.) This means that all interior components, like electrical connections, plumbing fixtures, cabinetry, furniture, etc. could affect the cost, when compared to those used in buildings where blast-resistance is not a factor.
An electrical finish is also a factor in the cost of a building. Some blast resistant buildings use surface mounted electrical, so all of the conduits is visible on the finished walls. While the look is more industrial, this allows easier access and is less expensive.
On the other hand, if the visual aesthetic of the building is essential, a blast-resistant building can have a more finished look, but it will affect the cost, both upfront and if repairs are needed at any point.
You must also consider if the interior space of the building needs to be ADA compliant. This will mean wider door frames, ramps, possibly lower counters or workspaces, and other considerations for those with disabilities.
Special accessibility for ADA compliance is also taken into consideration when figuring a bid for a blast-resistant building.
If pressurization or gas detection is required
If the hazardous elements present require the use of pressurization and gas detection, that is yet another element that affects the cost of the building. Consider that every element of a blast-resistant building is interconnected.
When you add gas detection, other elements of the building could be affected as well, because now you must consider, for example, how all the doors are sealed since each door could be an access point for toxins.
Adding pressurization means adding fresh air stacks and possibly other components, which could add some complexity to the project and this, in turn, affects the cost of the building.
For stacked buildings, the addition of stairs or scaffolding:
If you have a limited amount of space on your site, you might choose to use multiple buildings, stacked to accommodate the space. When this is the case, while you are saving valuable space, there will be an additional cost for stairs or scaffolding, and you may have to find those from another vendor.
State-specific requirements or third-party reviews
Depending on where your building is being placed, the authority over that location may have its own set of unique requirements. The authority having jurisdiction, or AHJ, could be at the local city or state governmental levels, or, it could be OSHA.
At the beginning of the planning process, these requirements will be considered, and there will be costs associated with compliance and with any third-party review that is required.
Some AHJ requirements could be things like the addition of fire sprinklers or alarms, specific kinds of plumbing fixtures or electrical finish, equipment to improve air quality, or control emissions, to name a few.
If you have negotiated an MSA (master service agreement) with the vendor
Having an MSA could affect the cost of the building in a “time is money” sort of way. An MSA ensures that terms and conditions have been negotiated upfront, so that time is saved in the decision-making process. This is particularly true when leasing blast-resistant buildings.
You can also make sure there is consistency among facilities and that all parties are on the same page when it comes to needs and requirements.
When you’ve experienced excellent service, an MSA is a good way to ensure that the level of service is reached when additional projects are starting. This will help you build a relationship of reliable service with a trusted vendor.
The addition of change orders during the build.
It’s important to make sure that when considering the cost of a blast-resistant building, you are sure about the final plan and have considered all needs. Once a company gives you the estimate for the amount of time it will take to engineer and design your building, a particular effort has been given to ensure that it meets all requirements and can be delivered on time and within budget.
Some companies won’t mention during the estimating process that changes during the build will lead not only to a change in raw materials but additional costs for engineering. It must be determined that proposed changes won’t affect the building’s structural integrity.
Getting a quote quickly, with a proposed timeline that seems too good to be true, probably IS too good to be true.
If you end up changing plans during the build, you will most likely see changes that will add additional time and also unexpected costs.
- 7 -
What are the problems with blast-resistant buildings?
As a rule, many companies will avoid talking about problems with their products. At RedGuard, we acknowledge that there are potential problems with ALL products, and it’s been our experience that transparency serves the customer well as they research a decision of this size and magnitude.
In this chapter, you’ll find out about some of the challenges with blast-resistant buildings and their solutions. In no particular order, here’s what we’ve found:
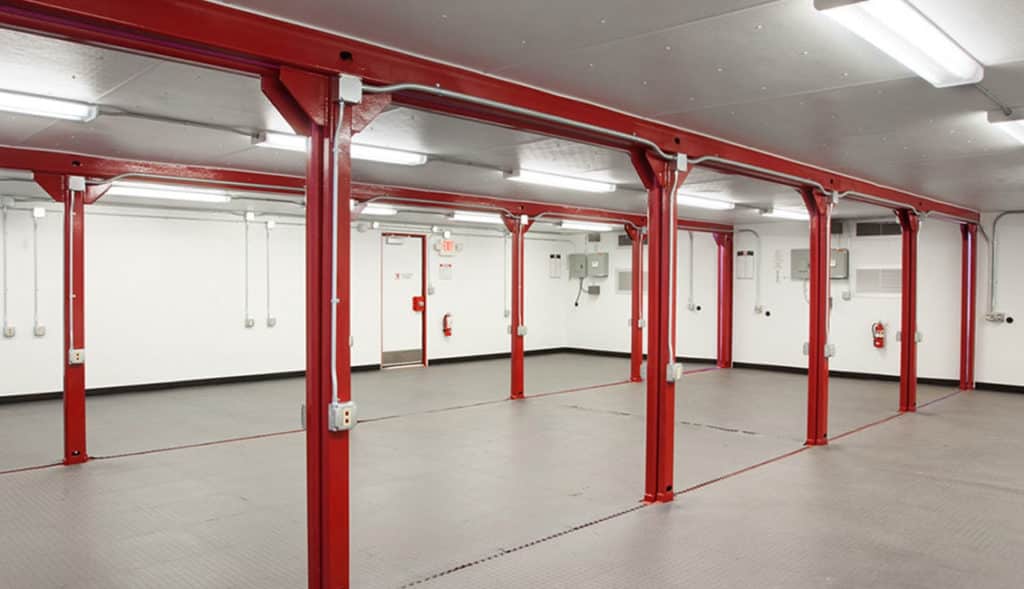
1. BLAST-RESISTANT DOORS ARE HEAVY!
Yes, blast-resistant doors are heavy, some weigh in at 450 pounds or more. It makes sense because they’re blast-resistant and made of heavy steel. The weight means that they have hydraulic mechanisms to make opening and closing them easier and to prevent slamming.
Because of these factors, blast resistant doors require regular maintenance to avoid sagging and out-of-alignment hinges or latches. Without proper care, the doors may not close properly, which could affect the building’s efficacy in a blast event. And, while it’s not common, a large, heavy door could cause injury if it’s not properly maintained and slams on a hand or foot.
WHAT CAN YOU DO?
To avoid problems with these doors, it’s important to note that they should never be left open to allow the free flow of traffic. Leaving the door open will allow the blast wave to enter the building in the event of an explosion.
Regular maintenance will also help prevent problems with blast-resistant doors and could include something as easy as a visual inspection to ensure that all fasteners are tight and that hinges and latches are functioning. We’ll talk about the maintenance of blast resistant doors in more detail in the next section.
2. WINDOWS MUST CONFORM TO NECESSARY BLAST RATING
The presence of windows in a blast-resistant building design has a direct correlation to its blast-rating. This is referred to as a single degree of freedom. Since a blast-resistant building is no stronger than its “weakest” component, the area the building is located will sometimes determine the presence and size of windows.
In general, blast-resistant buildings that are designed for placement in areas that may experience a higher psi blast will need to have smaller windows. These areas are places like a factory’s alkylation unit or other areas that have toxic gases or high-pressure pipelines.
Windows in these areas typically serve a utilitarian purpose, like monitoring an area, viewing a control, or interacting with personnel. Buildings that are the closest to dangerous processes may not be able to have windows at all.
If you are leasing your blast-resistant building, this might mean that you are at the mercy of the available inventory. For this reason, it’s best to begin planning well in advance to ensure the availability when windows are required. If a window is a desired amenity but is not required, you would then follow the best practice of using a building with a higher psi rating.
- 8 -
4 reasons for service calls on blast-resistant buildings
Along with problems, when researching a major purchase, it’s a good idea to look at what kind of maintenance will be required and what the most common reasons for service on a blast-resistant building are. It’s a great way to know about some of the costs that may be required down the road.
In this section, we break down four types of service calls for blast-resistant buildings that are important to know about before you buy. These are listed in no particular order and don’t necessarily denote that all buildings will have these issues.
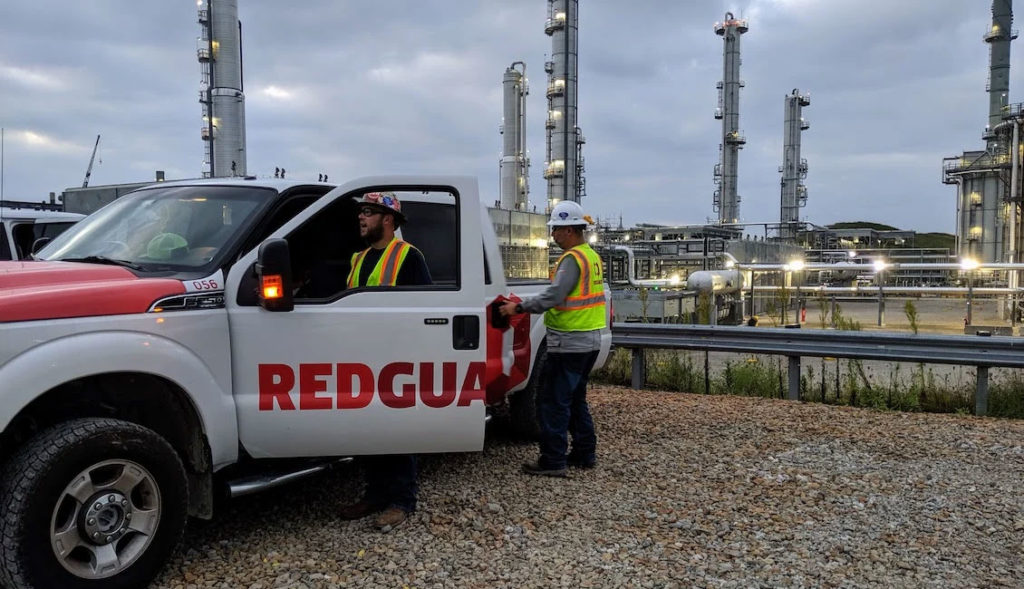
1. SERVICE FOR POOR HVAC/AC PERFORMANCE
Typically, when an HVAC/AC needs service, there is a filter that needs to be changed, and/or the coils need to be cleaned. Occasionally, the technician will also reload coolant or replace a sensor if it’s not functioning.
At RedGuard, our blast-resistant buildings are designed with specialized HVAC units to provide proper and sufficient heating and air conditioning for that building or unit size. We recommend that they run in an ambient setting of no lower than 73 degrees for cooling and no higher than 78 degrees for heat.
These units are often placed in locations with extreme temperatures that require the units to run more frequently than other commercial installations. Higher traffic in and out of the building will also cause it to run more frequently and need service more often.
Due to the environment, usually places with more dust and particulate in the air, the filters should be changed regularly, preferably every thirty days. In hot, dusty climates or where debris is more common, they may need to be replaced even more often.
2. MAINTENANCE ON BLAST-RESISTANT DOORS
A visual inspection of blast-resistant doors should be done every 60 days, or more often in high traffic areas. The visual inspection will include checking these details:
- Does the door seal correctly or have issues with slamming? Those are signs it needs to be serviced.
- Are the hinges still aligned properly? Because of its weight, the door may need to be realigned on its hinges or replaced.
- Do the door handles need to be tightened or replaced?
- How is the viscosity of the fluids in the door’s hydraulic mechanisms? In areas where temperatures are subject to change, the viscosity of fluids could be affected, causing doors to slam or have difficulty latching.
If you’ve decided to take on this maintenance yourself, you’ll need to know what to look for and how often. An effective service team will be ready to either guide you through the process or come out to make regular inspections during building maintenance.
And, while the doors are heavy, it’s important to remember that they are a factor in saving lives. Doors on blast-resistant buildings should never be propped open. The amount of wear and tear on the doors when they weigh 450 to 800 pounds, and the amount of traffic going through the doors in one day are significant factors in these repairs.
3. ISSUES WITH FLOORS OR CEILING TILES
Issues with floors and ceiling tiles that need to be replaced are another cause for service, though these problems are seen less frequently than the previous issues mentioned.
The nature of the work in and around blast-resistant buildings calls for heavy footwear. Heavy boots will track dirt, mud, or other particulates into the buildings. That can loosen or displace tiles.
Extreme temperature variances can be another issue for floors. Excessive heat may cause the flooring to warp or buckle, and cold temperatures may loosen adhesive. These issues are important to repair so that you can avoid the risk of someone tripping and falling on a loose floor tile.
Some blast-resistant buildings may use a painted floor surface with a texture added in to make them non-slip. While this flooring won’t have the issues above, they may require resurfacing at some point to maintain their non-slip texture.
Ceiling tiles will also occasionally need to be replaced if they become soiled from poor air quality, or due to water damage from water. (See the next issue!)
4. WATER LEAKS IN MULTI-SECTION BUILDINGS
Water leaks in blast-resistant buildings do happen occasionally. This isn't an issue that is seen frequently, it's not even among the top reasons for service calls, but it's worth mentioning so that there are no surprises.
The silicon and joiner material used when attaching or bringing two buildings together is also sensitive to ambient temperature, and there can occasionally be issues with adherence to the surfaces of the two buildings being joined.
Sometimes these joints can experience leakage during heavy storms. When this happens, you should call a technician to inspect the surfaces and repair the water leak, and any resulting damage to the interior.
- 9 -
Making choices on a capital project
Often, the purchase of a blast-resistant building is part of a specialized capital project. That doesn’t have to mean a complicated custom project. Recently, the addition of “pre-engineered” buildings added some flexibility to capital project decisions.
This chapter goes into the differences between a custom blast-resistant building and a pre-engineered blast-resistant building, as well as scoping out how to decide which choice works best for you.
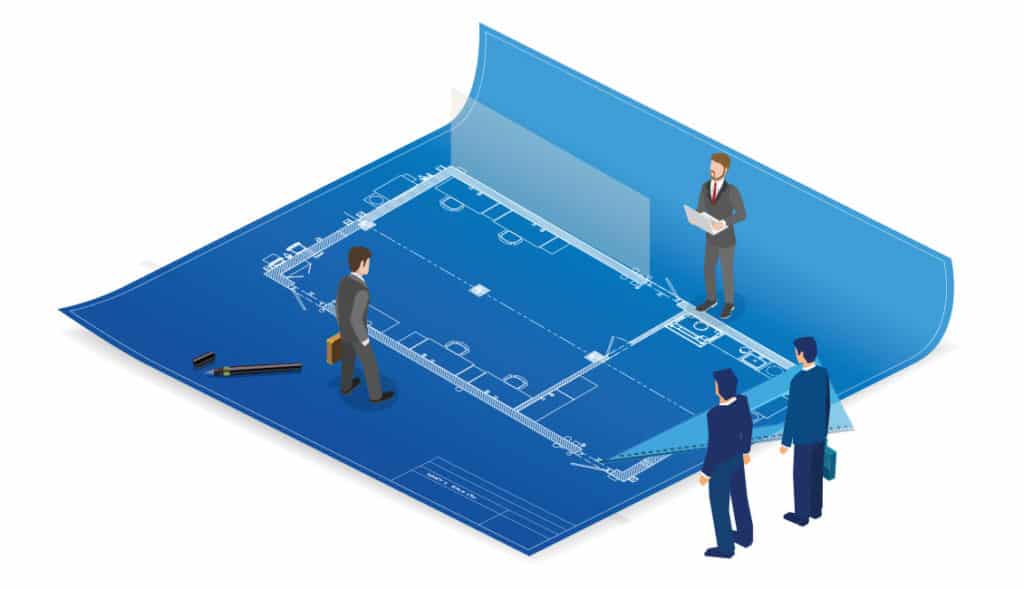
CUSTOM OR PRE-ENGINEERED? A COMPARISON.
CUSTOM
WHAT IS A CUSTOM BLAST-RESISTANT MODULAR BUILDING?
As it sounds, a custom blast-resistant modular building is a made-to-order blast-resistant building that follows exact specifications for a capital project. It could be a complex building that combines uses, like a control room, conference rooms, offices, and restrooms - all in one building, made up of several blast-resistant modules. It may incorporate a specialized HVAC system, positive air pressure (to keep clean air in, and contaminants out), or any number of special needs. As a blast-resistant building, all internal elements will be vetted for safety, and the building itself will have a hazard rating that matches the needs of the project. As a modular building, the majority of the work is completed offsite and there may be several rounds of changes, and engineering to be considered. A project manager will keep track of all the necessary communications back and forth on your custom project. Once the work is finished, it will be shipped to your location, carefully placed, assembled, and finished. Typically, in a modular build, you can get the same amenities that you would find in a stick-built (traditionally built) building.
ADVANTAGES OF A CUSTOM BLAST-RESISTANT BUILDING
Now that you have a short description of each, let’s weigh the advantages of opting for a custom blast-resistant building for your capital project.
1. YOUR OPTIONS ARE COMPLETELY OPEN
The main advantage of a custom blast-resistant building is that you get exactly what you want. If your project is complex, that means you won’t have to compromise a thing. If you need a very tall building, to accommodate lowering the ceiling for duct-work, that is easily done. If your control room’s specifications require a platform floor to hide wires or other computer/communications elements, no problem! If you need exactly six offices that are of a specific non-standard size - you can get it!
2. GET THE EXACT HAZARD RATING THAT YOU NEED
Another advantage to a custom blast-resistant building is that the hazard rating can be exactly to the number called for in your facility siting study. So, if you only need a 1, 2, or 3-psi building, you can get exactly that! You also may be able to incorporate shelter-in-place elements that you might not be able to get in something that has a predetermined layout. This might be elements like gas detection, fire protection, or air filtration.
DISADVANTAGES OF A CUSTOM BLAST-RESISTANT BUILDING
When someone is trying to sell you something, they’re going to shy away from talk of “disadvantages.” But we look at disadvantages differently. We realize that each one of these options (custom or pre-engineered) will be a better choice for different people. We’d like to help you sort that out. Here are some of the reasons that a custom build might not be for you.
1. CUSTOM BUILDINGS MAY COST MORE
Unlike some custom products, when it comes to a RedGuard blast resistant building, there is no automatic mark-up just because the project is custom. We know that for capital projects, time IS money and that’s the major differentiator. So, a custom building may cost you more in time resources. Some capital project managers are turned off by the lead time on custom projects. It’s understandable when they’re in a situation of having a budget, but need to spend it quickly before things change! Once a company is acquired or sold, all bets are off when it comes to a project that was in the making. For many in our industry, spending that budget quickly is paramount.
2. MORE DECISIONS TO MAKE / MORE COMMUNICATIONS / MORE APPROVALS
If you’re creating something custom, that means there are more options and more decisions to make. And, depending on your approval process and the number of people involved, that might mean more communications that need to happen and a waiting period for each one. Going back to the concept of "time is money," this may again be a detractor. Our Project Managers are skilled in communicating with customers for custom projects, but we know that the more people involved when approvals are needed, the more likely to add time to the project. We are always respectful of the time it takes to fulfill a custom project, but we acknowledge that they take more time.
PRE-ENGINEERED
WHAT IS A PRE-ENGINEERED BLAST-RESISTANT BUILDING?
As mentioned, a recent entry into the blast-resistant building market is that of “pre-engineered” modules. These are similar to custom blast-resistant modules in that they are “suite-quality” buildings, with construction completed off-site, and then delivered and finished.
Suite-quality refers to the level of finish in things like walls, electrical systems, plumbing (if present), and even some of the other internal elements of the building. You can expect that “suite-quality” will be of higher quality than that from a rental fleet.
With pre-engineered, the customer looks over available floor plans and matches them to their needs. The elements that make the building blast-resistant, like the “rib-cage” structure of the external walls and steel-reinforced doors are still present in a pre-engineered building and there are several standard configurations available, all with completed plans and engineering. The build starts once the layout is chosen and needs are discussed.
ADVANTAGES OF A PRE-ENGINEERED BUILDING
Now that you know some of the advantages (and the challenges) of a custom building, let’s take a look at the advantages for pre-engineered buildings.
1. HAZARD RATINGS WITH A HIGHER PSI
When a building is a standard design, that means it has to accommodate a greater number of users and circumstances. That means with a pre-engineered building, it may already be designed to withstand a greater blast load. That is true of our RediSuite line, for example, which has a hazard rating of 8 psi/200 msec. That means you are getting more protection for your money. This may seem like an irrational thing to think of as an advantage if you only need 2 psi, for example, but when you look at the long term, it could work out in your favor. Things change all the time on worksites, including the boundaries of a hazardous zone. When you get a facility siting study done in the future, that area could require more protection. It could be that processes have changed and that control room that once only required a building rated for a 3 psi blast, now requires more. It’s always good to have more protection than you need.
2. PRE-ENGINEERED SAVES TIME
We’ve used the word “time” in this piece enough to emphasize that we get how important it is. Our buildings are designed using a proven blast-tested design. When you choose pre-engineered, you will shave weeks off of the process by simply choosing your preferred layout from a variety of standard options and then outfitting it for your capital project. The standard options are created by evaluating the standard options that customers in the industry selected most often and making floor plans to fill those needs. Our pre-engineered modular buildings have proven to be very popular among midstream facilities, but have also found homes on downstream refineries as well.
DISADVANTAGES OF A PRE-ENGINEERED BLAST-RESISTANT BUILDING
There’s that word again - disadvantages. We’ve struggled in this article with the term disadvantages because both of these building types are top of the line and will be valid for specific use cases. But, of course, there could be elements that mean it’s not the right choice for you. The following “disadvantages” are some of the reasons that you might decide to take pre-engineered off your list.
1. HEIGHT OF A PRE-ENGINEERED BLAST-RESISTANT BUILDING
With a standard configuration, you may need to look at your needs and decide if you can fit them into the layouts that are available. One thing that can’t change is height. A standard pre-engineered building starts with a greater height than most fleet buildings, but at 11 feet may still not reach the height that you require, if you need dropped ceilings or computer platform floors.
2. STANDARD CONFIGURATIONS
We’re able to accommodate any requests to make a pre-engineered building fit your specifications, but there are some projects that are much more complicated than pre-engineered will allow. In those cases, a custom blast-resistant building is the way to go. Pre-engineered layouts won’t work for every project, nor should they. But it’s always worth talking to your vendor to see what elements can change and what can not.
3. HAZARD RATING COULD BE TOO LOW
If the requirements for your project require a higher hazard rating than the pre-engineered buildings that you are considering, that’s an element that cannot change and will automatically take pre-engineered off the table for you. In other words, if your project requires a 10 psi building, and the pre-engineered line has a hazard rating of 8 psi, that means it will not work for your use and you should consider a custom blast-resistant building.
WHICH IS BETTER FOR ME?
Weighing all of these differences, we hope that you are now more informed about two excellent options for your capital project. One of them may already be a standout for you.
A custom blast-resistant building is your starting point if:
- If you have a highly specific layout in mind and many specialized needs that can’t budge.
- You need a building that has a hazard rating of a very specific rating.
- You have the time to work within the time frame that a custom project will require.
Start by considering your pre-engineered options if:
- You have a little bit of room for flexibility in your layout.
- You can work with a hazard rating of 8 psi (even if you require less).
- Your time is of the essence and you’d like to get this project rolling as quickly as possible.
- 10 -
When should you lease a blast-resistant building?
If buying a blast-resistant building is not the solution you’re looking for, but you still need the protection that comes along with it, many companies offer a range of blast-resistant buildings that can be leased temporarily.
This chapter is all about “what you need to know” list about leasing a blast resistant building that can help you get an accurate quote and plan around potential obstacles.
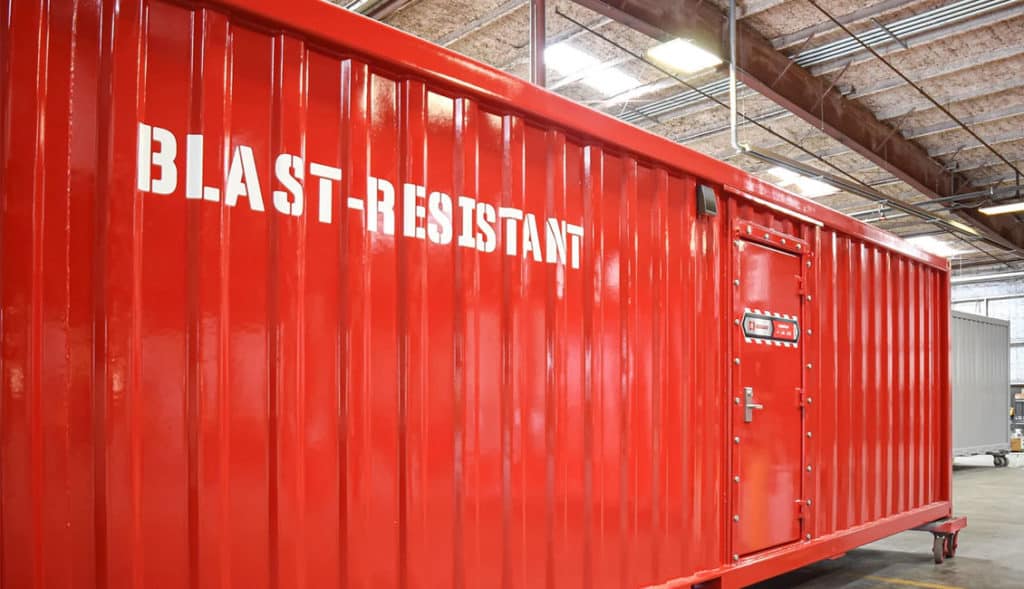
While the use of blast-resistant buildings is widespread, there are still many in the industry who have not utilized modular buildings during outages and projects. Instead, they stage operations outside the facility and transport labor in and out. Over the past ten years, the use of modular blast-resistant buildings in refineries and chemical plants has dramatically increased due to their wide range of benefits. Both permanent and nonpermanent use of blast-resistant buildings has proven to be cost-effective, efficient, and reliable throughout many spaces in the oil and gas industry.
LEASING BLAST-RESISTANT BUILDINGS: WHAT YOU NEED TO KNOW
If you have not leveraged the advantages of blast-resistant buildings on-site yet, the following list is what you need to know to get started. Providing this information to your supplier will set up an excellent opportunity to generate an accurate quote and help you identify and plan around potential obstacles.
Understand your needs: Blast-resistant buildings are excellent structures for cafeterias, break rooms, tool sheds, equipment storage, and spaces for offices, permitting, or security. Identifying specific operations and trades that drive improved cost-efficiencies while being located in the hazard areas is a starting point for understanding their importance.
Capacity: Headcount drives the quantity of blast-resistant buildings needed. The dimensions of blast-resistant buildings are wide-ranging. There are small 8-foot units suitable for one to two occupants and “multi-section” complexes that can be merged into single buildings hundreds of feet wide. Knowing your headcount tells you what size building is required.
Hazards: Recognizing the hazards and specifying correctly rated blast-resistant buildings are critical for creating safe and compliant spaces. When it comes to blast-resistant buildings, there is significant data and engineering that ensure the correct units meet or exceed the site’s hazards.
Access: Standard blast-resistant buildings are large. Access for truck delivery and crane offloading should be planned. That starts with your vendor understanding curfews, limits, and clearances on public roads leading to a facility. Then, identifying any overhead or width clearances inside the facility is critical.
Layout: If space is limited in the work zone, proper sequencing and layout of units optimize the space. There are seemingly unlimited configurations for a blast-resistant building’s long, rectangular shapes. Ensuring the buildings arrive on-site in the correct order is a critical element. In the staging portion of a project, there is typically not much lay-up space available to leave large buildings sitting temporarily.
Utilities: Many blast-resistant buildings require an electrical supply and communication connections for LAN or WAN networks. Additionally, units with working plumbing require a potable water supply and waste connection. On short-term projects, power can come from generators or site supply. Networking into a facility's communication network is generally straightforward. Identifying utility sources and their locations is a critical piece of the planning process.
Timing: Establishing start and end dates will provide cost-certainty and allow the blast-resistant building supplier to adequately plan for availability, delivery, and pickup. High utilization during certain times of the year can limit availability. Sharing your project’s anticipated start and stop dates early in the planning process will offer you greater selection and availability.
Demobilization: Like all projects, having a vision for a strong finish ensures a clean, organized completion. Efficiently disconnecting utilities and cleaning the units allow for an organized, staggered schedule of trucks arriving to remove units from the site as quickly as the crane and rigging crew can safely lift, place and secure each unit.
- 11 -
5 questions to ask before choosing a blast-resistant building
Before pulling the trigger on purchasing or leasing a blast resistant building, this section gives you a guideline of the important questions to ask your vendor that can save you from headaches.
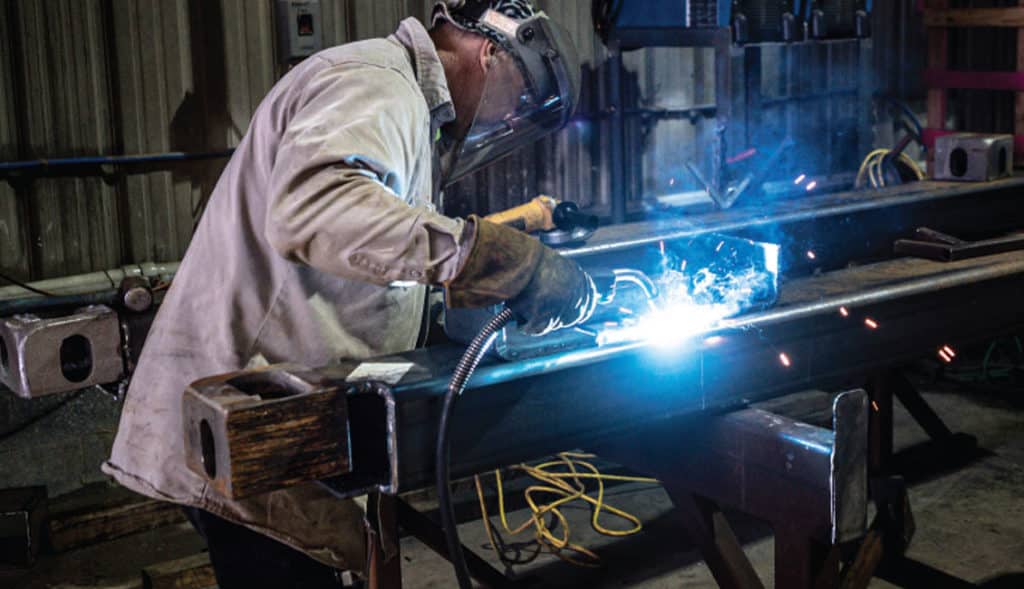
1. WAS THE MODULE DESIGNED AND TESTED BY A BLAST EXPERT?
The science of blast-resistant building design is no longer a new science, but it is still true that not all blast resistant building makers have tested their designs. Make sure your blast-resistant building design has been taken off the drawing board and successfully blast-tested under the supervision of a well credentialed engineer. There's no shame in asking about your vendor's "experts" - who they are and about their training and background. Do they have years of experience in the science of blast-resistant design, or did they take a three day course to qualify them?
2. ARE BLAST TEST REPORTS SPECIFIC AND CONCLUSIVE?
There are many interpretations of the term blast-tested, but a successfully blast-tested building has the proven ability to actually save lives. Pay special attention to duration and psi ratings when you review blast test reports because different applications call for different specifications. A laboratory blast-resistant building placed next to a blowdown stack should carry a higher rating, such as 8 psi, while a guard shack placed at the perimeter of your facility may only need a 3- to 5-psi rating.
3. WAS IT BLAST-TESTED FOR NONSTRUCTURAL/ STRUCTURAL COMPONENTS?
If a structure survives a blast but its interior walls, lights or other fixtures create shrapnel, the risk of casualties is still high. Always ask blast-resistant building vendors to provide data and rationale for nonstructural items including wall and ceiling finishes, light fixtures, plumbing fixtures, cabinets, placement of open shelving and placement of any intake points.
4. CAN THE FOLLOWING INFORMATION BE PROVIDED?
The following items are too technical to cover in the context of an online article but should be on your list of discussions to initiate with any blast-resistant building vendor.
Was it tested in a free field environment?
Was a P-I (pressure-impulse) curve generated to show the blast-resistant building's response over a wide range of blast loading?
5. DOES THE BUILDING'S RESPONSE LEVEL DEMONSTRATE ITS CAPABILITY TO SAVE LIVES?
If a close examination of a manufacturer’s data demonstrates a high-response result, this is not the structure you want protecting your personnel. Response level ratings have been established to predict the extent of repair resources needed after an explosion. Here's the key, as we’ve mentioned: high response equals high damage. It's crucial to study the response level table, then take a very close look at any blast-resistant module's response rating for a given duration and psi (as proven through actual blast testing).
- 12 -
What happens after the sale?
All about project management
Another thing to consider just before making your purchase is what happens after the sale. Is it just a matter of waiting? Will you get updates? Will the timeline change? Is my sales rep still the main contact?
The next step is project management and experienced vendors and manufacturers of blast resistant buildings should be able to paint a picture of what that process will look like.
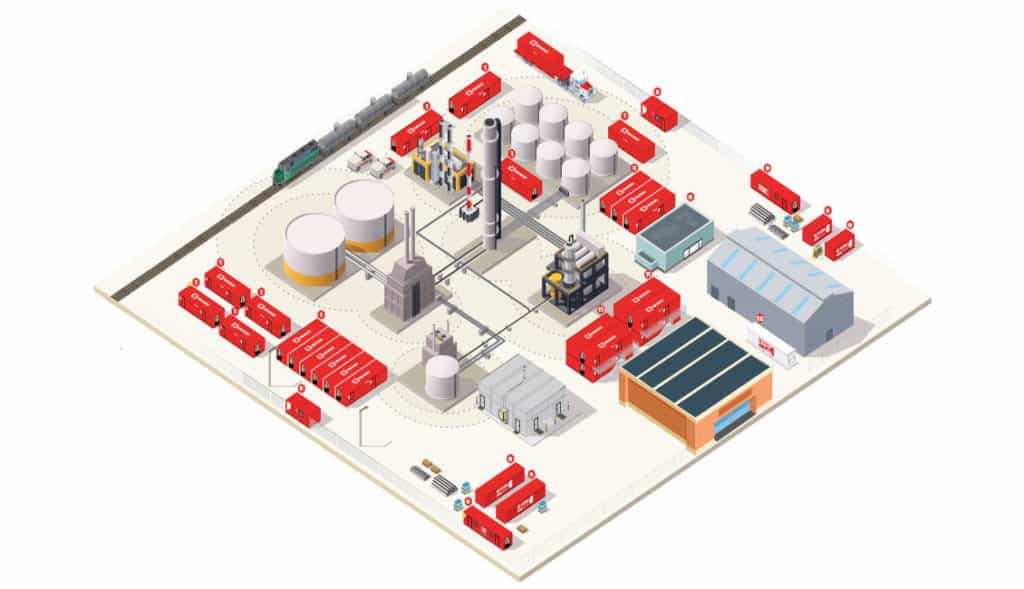
MOVING INTO PROJECT MANAGEMENT
Once a purchase order (PO) is received, the project is handed over to the project management group. At that time, a purchase order review begins to make sure that the company can/will accept the purchase order.
Not all POs are accepted immediately. Sometimes the blast-resistant building manufacturer requires changes in the contract language, or there could be details to be clarified before the PO is formally accepted.
Occasionally, some new specs may show up in this stage. For example, the purchasing agent may not have clarified the type of HVAC system required or whether the system should be redundant. Before the PO is accepted, the building vendor will send it back with language defining these types of details, and the customer will need to approve the additional details.
Depending on the complexity of the changes, and the responsiveness of those involved, getting the PO approved could take between a few days and a few weeks. The project manager will do what they can to ensure the process keeps moving until both parties sign-off on the PO.
THE KICK-OFF AND DESIGN STAGE MEETINGS
Once the purchase order is formally accepted, the floor plan is emailed to the customer for review, and an initial kick-off meeting is scheduled.
The kick-off meeting gives the salesperson the opportunity to introduce the customer to the project manager, and for the project manager to begin talking about expectations for the project. During the kick-off meeting, the customer has reviewed the floor plan in advance, allowing for more design conversations to begin. In this meeting, there will also be a detailed review of the architectural, mechanical, electrical, plumbing, structural, and blast components of the building. Additional meetings may be required for each of these components of the blast-resistant building.
Once the project is under the care of the project manager, the original salesperson will be relatively hands-off unless their assistance is needed. For example, their assistance may be required to discuss change orders or commercial changes, which occur when there are customer-driven changes that result in an increase or decrease to the contract price.
Depending on the customer’s preferences, calls will be set up weekly, or updates can be given periodically by email. The important part is to keep an open channel for communication flowing.
BLAST-RESISTANT BUILDING TIMELINES
There’s no real way to narrow down how long a blast-resistant building project will take since the timeline will vary based on factors like building size, design complexity, material availability, state-specific approval processes, and project backlog.
Project sizes can vary from simple single unit buildings, which may be ready in a matter of weeks, to large multi-section complexes which could take months, or the better part of a year. The best way to find out the timeline is to ask about the specific details for your project.
As a general rule, ask questions. How will the project be managed? What happens if we have change orders? Will this change affect my projected delivery date?
In most cases, project management begins when the order is accepted and ends when it leaves the vendor’s production facility. Once the blast-resistant building is installed, regular maintenance and any issues that come up are handled by a qualified service department.
CUSTOMER APPROVAL AND FINALIZING DESIGNS
Once the kick-off meeting has occurred, initial introductions have been made, and the customer signs off on the floor plan, then things begin to move forward. It’s important to have an approval process in mind on your end when approval is required at other stages. This will help the process run in a timely manner.
Other meetings that will need to occur and places where other approvals may come into play will be when discussing the architectural, mechanical, electrical, plumbing, structural, and blast components of the building. Each of these components will need to be reviewed and approved using detailed pdf files. These drawings will call out the placement and specifications for each of these elements, which were not detailed on the floor plan.
THIRD-PARTY APPROVAL FOR BLAST-RESISTANT BUILDINGS
Each build-site is different as far as requirements for blast-resistant buildings. Some states have strict environmental guidelines (California comes to mind), some follow another set of standards, like OSHA or other federal, local, or regional guidelines.
Your blast-resistant building manufacturer will be responsible for ensuring that the building meets all requirements of the local authority having jurisdiction (LAHJ) and will set up any third-party reviews that need to happen.
These requirements could add things like fire sprinklers, devices to improve air quality or emissions, or any number of details meant to protect the occupants of the building. It is the responsibility of the vendor to know and expect these requirements.
CONSTRUCTION OF THE BLAST-RESISTANT BUILDING
Because they are modular in nature, the construction of blast-resistant buildings happens before they ever get to your site. This is one of the greatest benefits of modular construction.
In short, this means there’s much less of an impact on your site operations. There’s no period of downtime for the space the building will occupy. There’s no working around the mess of a construction site. There’s no re-routing of trucks.
During the construction phase, the customer will get updates as needed, including progress photos. There’s no way to nail down how long the construction of a blast-resistant building will take because each project is different. It’s all dependent on the construction queue of the vendor, the size of the building, and the complexity of design and elements.
A typical build, for example, a simple three-plex or smaller, may take 16-20 weeks from the time drawings are approved. Other complex projects will take more time. Your vendor should be able to talk in more detail about this, based on the specs of your individual project. There are occasionally ways to expedite builds, but it’s not a good practice to rely on that to happen.
The last thing to happen while the building is still at the vendor site is the factory acceptance test. The building is put together at the facility, just like it would be on the customer’s site. Some customers may choose to do a final onsite walk-through; others may give approval based on photos of the finalized building. This can typically be done in a day.
TRANSPORTATION AND INSTALLATION
Once the final walk-through has happened, there will be no time wasted before the build is on the road. If the building is a multi-plex, it could take several trucks to get it to its final destination.
Some companies have their own transportation fleet, while others rely on outside sources. And some will use a combination of their own trucks and third-party transportation sources.
PROJECT MANAGEMENT CHALLENGES
According to the project managers at RedGuard, working through the design process without delays is the biggest challenge in managing blast-resistant building projects.
Designing a building requires a lot of information and input from the customer. Sometimes there is information that is not available during the bid phase.
AWAITING DETAILS
Examples of some information that may not be available before the PO is issued are things like the actual electrical load requirements for equipment that is supplied by the customer, the expected use for each room in the building, and final details like color or finish selections. Waiting on these things can slow down the initial design process.
GETTING EVERYONE INVOLVED
Another hold-up is that sometimes the person who’s been involved on the customer side, the purchasing agent, isn’t the end-user of the blast-resistant building. Once the end-users become involved, they may have valuable information or knowledge of the project that will require changes during the initial review. For this reason, it’s helpful when decision-makers and the building’s users are both involved during the bid process, so all details are resolved prior to project award.
CHANGE ORDERS
Change orders are a fact of life in the management of blast-resistant building projects, so it’s not the worst-case scenario when they come up, but avoiding them will always save you time and money. Following the advice here, as well as keeping the lines of communication open, and the team informed, will serve you well.
WRAPPING IT UP
At RedGuard, we design and build blast-resistant buildings and have been doing it since 2005. All the related details are on our minds every day, for at least 40 hours a week, but we know that our customers have more to think about. That’s why our team of experts, in Sales, Estimating, Engineering, and Project Management, are ready and willing to answer your questions and consult on your project.
No matter how much experience you have with capital projects or turnarounds, let’s start talking about your goals and see if it makes sense to put a RedGuard blast-resistant modular building on your worksite.
No two hazardous worksites are alike, so no two blast-resistant projects are alike. Our expert team can help you start planning your project to save you time, money, and, most importantly, lives
With this in mind, it is important to note that blast-tested buildings are usually given specific psi ratings. Knowing what rating your facility needs, will depend on many factors, such as the type of structure, the likelihood that it will experience a blast event, and its proximity to different assets, equipment, and materials. For example, a laboratory BRB that is near a blowdown stack might need an 8 psi rating, while a structure that is located closer to the perimeter of your facility might only need a 4 or 5 psi rating. (These are hypothetical and don't represent actual recommendations.)